Theory of Constraints
The Theory of Constraints (TOC) is a significant methodology within project management that identifies the most substantial limiting factor (i.e., constraint) that stands in the way of achieving a goal and systematically improves that constraint until it is no longer the limiting factor.
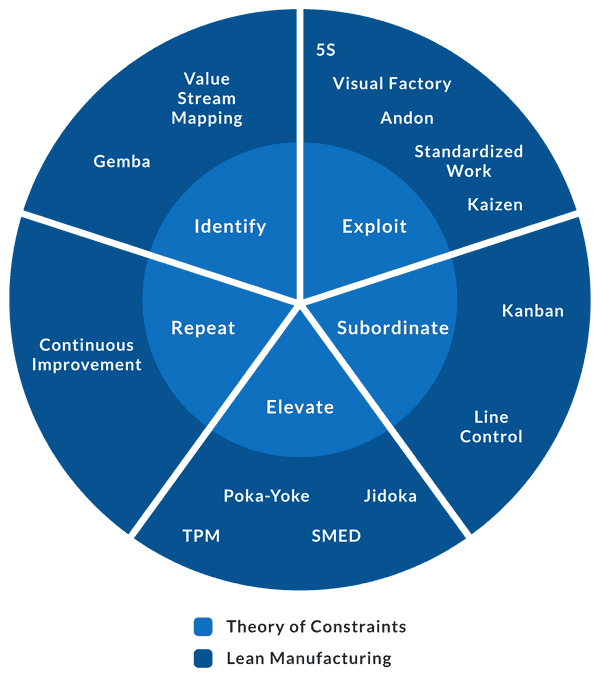
What is a Constraint?
A "constraint" refers to anything that limits a system's performance relative to its goal; constraints can be physical or non-physical and include any element, factor, or resource that restricts the output, efficiency, or effectiveness of a process.
There are different kinds of constraints and usually are divided into:
Physical Constraints
There are tangible limitations within a system, such as machinery capacity, limited floor space, or insufficient raw material.
For example, in a manufacturing process, a physical constraint could be a machine that operates slower than others, thus limiting the overall production rate.
Non-Physical Constraints
Are intangible factors that affect the system's performance, including policies, procedures, or even organizational culture that hinder productivity?
An example might be a company rule that requires multiple approvals before taking action, which slows down the process.
Bottlenecks
While all bottlenecks are constraints, not all constraints are bottlenecks :)
A bottleneck specifically refers to a point in the process where the flow of operations is significantly slowed down or impeded, leading to a backlog.
Resource Constraints
Occur when there is a lack of necessary resources, such as labour, capital, or time, which restricts the system's ability to produce more output.
For example, a project team might be unable to progress at a desired pace due to the limited number of skilled workers.
What is the Theory of Constraints?
Developed by Dr. Eliyahu M. Goldratt in his 1984 book The Goal: A Process of Ongoing Improvements. Goldratt (March 31, 1947 – June 11, 2011) was an Israeli physicist, theorist, and management consultant, his work has had a profound influence on the fields of project management, manufacturing, and operations.
Goldratt earned a Bachelor of Science degree in physics from Tel Aviv University, and later pursued his graduate studies in the United States, obtaining a master's degree and a PhD in physics from Bar-Ilan University, focusing on solid-state physics. Despite his initial scientific career, his interest gradually shifted towards business management, leading to his groundbreaking work in process improvement.
The “Goal” book is presented in the form of a business novel, following the story of a factory manager struggling to save his plant and his marriage, through the narrative, Goldratt introduces and explains the core concepts of TOC.
The core idea of TOC is that every process, whether in manufacturing, business, or even personal life, is limited by bottlenecks or constraints that prevent it from achieving higher performance.
According to TOC, the focus should not be on maximizing local efficiencies but rather on identifying and improving these constraints, thereby increasing the throughput of the entire system.
TOC encompasses several key concepts and tools:
- The Five Focusing Steps:
Identifying and improving system constraints through specific steps.
- Throughput Accounting:
An alternative to traditional cost accounting, focusing on the overall throughput (the rate at which a system generates money through sales).
- Drum-Buffer-Rope Scheduling:
A production planning methodology that derives from the TOC principles.
Throughout his career, Goldratt wrote several books and numerous articles and continued to develop and refine the Theory of Constraints.
He founded the Avraham Y. Goldratt Institute, named after his father, to promote TOC learning and implementation around the world, his ideas continue to influence and inspire a generation of thinkers and managers looking to optimize and improve their operations.
Goldratt and the Long-Term survival theory of the firm
According to Eliyahu M. Goldratt, the only thing that can guarantee the long-term survival of a firm is its ability to generate money, specifically through continuous improvement and focusing on throughput.
Goldratt's primary focus was on how businesses can sustain and increase their profitability over time, which he outlined through the concept of throughput accounting in his Theory of Constraints (TOC).
Throughput is defined by Goldratt as the rate at which the system generates money through sales, not merely about maximizing production or minimizing costs, but rather optimizing the flow of products and services through the entire system ensuring that every step adds value and contributes to the end goal.
The principles of the Theory of Constraints advocate for focusing on constraints that limit throughput and systematically improving them to increase overall system performance.
Goldratt argued that traditional cost accounting measures can often mislead management into making decisions that are not in the best interests of the firm's long-term health. Instead, he proposed throughput accounting, which focuses on three main measures:
1. Throughput (T): Money generated through sales.
2. Inventory (I): Money tied up in things the system intends to sell.
3. Operating Expense (OE): Money spent on turning inventory into throughput.
The goal, according to Goldratt, is to increase throughput while simultaneously reducing both inventory and operating expenses.
The approach shifts the focus from cost reduction to a broader perspective of enhancing the flow of products and services, which, in turn, enhances the firm's ability to generate profit and ensures its long-term survival and growth.
The application of the Theory of Constraints, Five Focus Steps
The application of TOC involves five focus steps essential steps, often remembered by the acronym "FOCUS":
1. Identify the Constraint
Determine the most critical bottleneck that is limiting the process or system from achieving higher performance or throughput.2. Exploit the Constraint
Maximize the efficiency of the constraint without incurring high costs. This could mean making the most of the available resources at the bottleneck.3. Subordinate Everything Else
Align the entire system or other processes to support the needs and limitations of the identified constraint, ensuring that the constraint’s performance is not hindered by other factors.4. Elevate the Constraint
If the constraint cannot be adequately addressed by exploitation and subordination alone, further actions are required to elevate (or break) the constraint, such as adding resources or reducing demand.5. Continuously Improve
Once a constraint is addressed, the process does not stop. The system is reassessed, and a new constraint may emerge, which needs to be managed using the same process.
Constraints in Project Management
In project management, constraints are factors that limit the options available to manage and deliver a project, these limitations can impact various aspects of a project, such as its scope, timeline, budget, and quality.
Mainly I choose to divide the constraints in Project Management into 5 categories, moreover, it is divided in three, often called the Triangle of constraints;
1. Scope Constraints
Are relate to what must be done to produce the project's end results, includes the specific tasks, deliverables, and standards required to complete the project.
Scope constraints define the boundaries of the project.2. Time Constraints
Involve the timeframes within which the project must be completed.
Time constraints dictate the schedule for the project's milestones and deadlines.3. Cost Constraints
Encompass the financial resources available for the project.
Cost constraints set the budget within which the project must be managed.4. Quality Constraints
Specify the standards and criteria needed to satisfy the customer's requirements. Quality constraints ensure that the deliverables meet a certain level of performance or expectation.5. Resource Constraints
It involves the availability and allocation of resources needed to execute the project, including personnel, equipment, and materials.6. Risk Constraints
Include potential external or internal risks that could impact the project’s execution or outcomes, managing risks involves identifying, analyzing, and mitigating risks throughout the project lifecycle.
Examples to Illustrate the Theory of Constraints
Consider a software development team that cannot deliver features fast enough due to limited testing resources.
The testing phase is the constraint, by focusing on this constraint—perhaps by automating more tests and optimizing the testing process—the team can deliver features faster.
Another example is in manufacturing, where a specific machine might be the slowest point in the production line and limit the overall output.
The focus would be on maximizing this machine's throughput (exploiting), adjusting production rates to match its speed (subordinating), and eventually increasing its capacity or adding more machines (elevating).
Predicting the Constrains
Not easy, but possible, predicting constraints in project management involves proactive identification and analysis to foresee potential bottlenecks and limitations that could impact the project’s progress.
Effective prediction of constraints is critical for avoiding surprises and managing project risks efficiently. Here are several strategies to predict constraints in project management.
No one has the Cristal Ball, but usually, patterns are repetitive in each project and company, due to the team being shaped or weak points of the StakeHolders or any BlackSwan around the corner, wherever by using these strategies, project managers can predict potential constraints and incorporate effective strategies into their planning and execution phases to mitigate or manage these constraints proactively.
Historical Analysis
Review past projects similar in scope and complexity to identify recurring issues or bottlenecks. Historical data can provide insights into typical constraints faced in similar scenarios, helping project managers anticipate and plan for similar challenges.Expert Consultation
Engage with experts who have experience in similar projects or domains.
These professionals can provide valuable insights based on their experiences, highlighting potential constraints that might not be obvious to someone with less experience.Risk Assessment
Conduct thorough risk assessments during the planning phase.
It involves identifying potential risks and evaluating their likelihood and impact on the project, by understanding risks, you can predict related constraints, such as resource shortages, delays, or regulatory changes.Resource Analysis
Evaluate the availability and capabilities of required resources, including team members, technology, and materials.
Analyzing resource limitations early helps in predicting constraints related to workforce expertise, material shortages, or technological challenges.Stakeholder Analysis
Identify and engage all stakeholders early in the project.
Understanding their interests, expectations, and influence can help predict constraints arising from conflicting requirements, approval delays, or changes in project scope.Scenario Planning
Use scenario planning to anticipate potential future conditions that could impact the project.
The method involves developing plausible future scenarios and exploring how they might affect project constraints. It helps in preparing for uncertain conditions that could constrain the project.Critical Path Analysis
Use project scheduling and management tools to identify the critical path of activities.
Analyzing the critical path helps in spotting time-related constraints and dependencies that could delay the project.Continuous Monitoring
Implement a system for ongoing monitoring of the project’s progress against its baselines.
Continuous monitoring allows for early detection of deviations that might indicate emerging constraints.
Connection Between Theory of Constraints and Lean Manufacturing
The TOC complements lean manufacturing, which focuses on eliminating waste within manufacturing systems.
Both aim to improve overall system performance through continuous improvement, while lean manufacturing emphasizes removing non-value-adding steps to reduce waste, TOC concentrates on optimizing the performance of the system’s bottlenecks, which indirectly helps in waste reduction by enhancing flow and throughput.
Combining Lean Thinking with the Theory of Constraints (TOC) provides a powerful approach to process improvement and efficiency in project management and operational systems.
Both methodologies aim to maximize value and performance, but they focus on different aspects of the production and management processes.
Lean and TOC involve using TOC to identify and manage bottlenecks and using Lean principles to eliminate waste throughout the rest of the system.
Combining Lean Thinking with the Theory of Constraints (TOC) provides a comprehensive approach to optimizing organizational efficiency and effectiveness. This integration allows businesses to tackle issues from multiple angles—focusing on both the critical bottlenecks that constrain throughput and the pervasive inefficiencies that can detract from overall performance. Let's explore how these methodologies can be synergistically applied for greater operational success.
Use TOC to Identify and Focus on the Bottleneck
The initial step in this integrated approach involves employing TOC to precisely identify the most significant constraints within the system. It is crucial because these bottlenecks determine the maximum capacity and efficiency of the entire operation.
Focusing on these constraints ensures that improvement efforts are concentrated where they will have the most substantial impact on performance. It’s a strategic move, directing resources and attention to areas that are critical for throughput enhancement, thereby optimizing the return on effort.
Apply Lean Tools to the Constraint
Once the primary constraint is identified, the application of Lean tools like Kaizen, 5S, or Value Stream Mapping directly at this point can significantly enhance its operation. These tools are designed to make processes more efficient, eliminate waste, and improve the overall flow.
Applying Lean methodologies to the constraint, the organization can ensure that this critical element operates as smoothly and efficiently as possible, thereby maximizing throughput at this bottleneck.
Apply Lean to Non-Constraints
While the focus of TOC on the bottleneck is crucial, Lean principles are applied more broadly to address waste and inefficiencies in other areas of the process. It ensures that once the primary constraint is optimized, other parts of the system are prepared to handle the improved flow without becoming new bottlenecks themselves.
The holistic application of Lean helps in maintaining a balanced and efficient system, reducing waste and improving flow across all operations, not just at the critical points.
Use Lean to Support Subordination
In TOC, subordination refers to aligning the entire system to support the needs of the identified constraint. Ensuring that all processes are streamlined and that waste is minimized, the overall system can effectively support the constraint, thus enhancing its performance and the performance of the system as a whole.
Every part of the process is attuned to the pace and needs of the bottleneck, facilitating a smooth and uninterrupted flow of operations.
Continuous Improvement Cycle
The integration of TOC and Lean culminates in a continuous cycle of improvement. With the primary constraint addressed, the focus shifts to identifying and resolving the next constraint, while Lean principles continue to optimize flow and eliminate waste throughout the system.
The iterative process not only helps to maintain optimal performance but also fosters a culture of continuous improvement and agility within the organization.
By utilizing both Lean Thinking and the Theory of Constraints in tandem, organizations can create a dynamic and responsive environment that not only addresses specific bottlenecks but also enhances the efficiency and effectiveness of the entire system; it does not just solve isolated problems; it transforms the way the entire operation functions, leading to sustained improvements and a competitive edge in the marketplace.